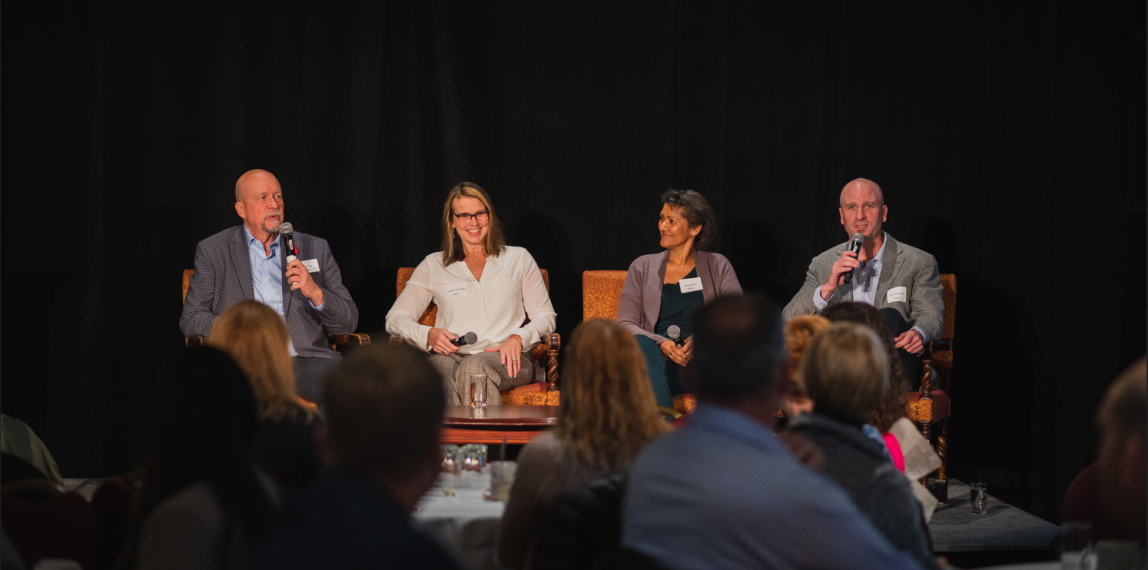
Mining Journal Intelligence interviews Larry Long for its Global Leadership Report 2022
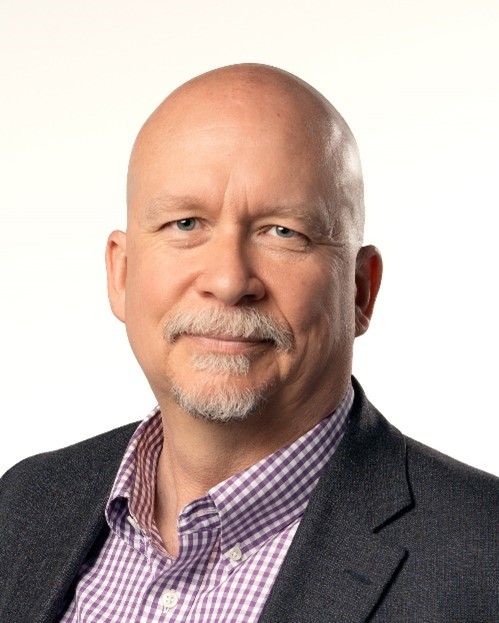
Larry Long, Senior Vice President, Operations of Nutrien’s Potash business unit was interviewed by Mining Journal Intelligence for its Global Leadership Report 2022 and discussed topics including COVID-19, technology, investments and culture – all under the overarching theme of safety.
The interview, provided by Mining Journal Intelligence, is below.
Safety has long proved a critical issue in the mining industry. Traditionally, it is interpreted as the protection of stakeholders exposed to the hazards associated with day-to-day mining activities and mitigating the risk of harm and injury. However, research produced by Mining Journal Intelligence over the past couple of years has shown the traditional interpretation is evolving faster than ever, not least with the onset of COVID-19 and innovative technologies.
The Global Leadership Report 2022 explores the broadening definition of Safety in mining through our Global Leadership Survey. The results prioritise and analyse key safety factors and developments both today and tomorrow from different stakeholder perspectives, supported by unparalleled industry guidance from interviews with C-suite executives of mining’s largest companies (>US$1bn market cap).
How has COVID-19 changed your understanding of safety?
It hasn’t really changed our understanding of safety, but it did force us to add another layer to our safety protocols. At the beginning of the pandemic, we didn't know what was going to happen to our operations to be quite frank with you. As a market leader in the production of fertilisers for agricultural crops, the government really wanted us to keep going because people need food. We focused on providing communication and education in order to keep our people safe and prevent the disease from spreading at our sites.
As we settled into the routine of dealing with COVID at our operations, we did start thinking about the mental health part of it. Initially, there was a lot of anxiety amongst employees working side-by-side. It was a question of whether they trusted their colleagues were doing the right things, not necessarily at work, but when they're away from work, to keep themselves healthy and so they didn't come to work and get their peers sick. Our people were worried about what might happen to them and their family if they took the virus home and didn’t realise they had it. They were also concerned about job security in the event things got so bad at Nutrien that we shut down operations. We did offer continuous pay during this time to take some of that anxiety away from people, which I think did help to some extent. But humans are humans; we have a variety of emotions and people process information differently.
As time went on, it became very important to check in with people. We were getting feedback around some employees feeling isolated. We worked closely with our team leaders to ensure they were checking in on their employees, asking them how they're doing, and whether there was anything they could help them with. It was also important to provide them with access to mental health professionals and ensure they knew what resources we had available if they felt overwhelmed by the situation.
How important is technology to improving safety?
We are investing a lot in technology. Of course, it improves productivity but also safety.
Tele-remote operations for our underground mines are a big focus because, for us, the serious injuries and fatalities often happen in the underground environment. We need to reduce risk exposure for our employees. It’s very preliminary stages but two of our sites are trialling tele-remote on surface. For example, I visited our Lanigan mine not too long ago and spoke to a couple of guys: two young employees and an older one who were doing tele-remote. I wanted to talk to the guy that was closer to my age – the older guy – because he didn't grow up with technology. What he said was, at the end of a normal shift, he would have spent all day in dust in the heat of underground. However, the tele-remote operation meant he was not only removed from this unpleasant environment but surprised since he actually had better information feeding to him on his cutting activities than he did when he was sitting underground. I thought it was quite amazing that a guy who’s 57 and didn’t grow up with technology, unlike his younger colleagues, was giving me this testimonial.
This type of technology takes away a lot of risk - though not 100%. It will definitely help to reduce serious injuries or, worse, fatalities that we've had in underground operations which are often around ground control, and ground falls. We know our next step is automated bolting and we’re looking at automating mainline conveyors where – because it’s such a manual job at present – we get a lot of injuries like pinched fingers, strains, pulled muscles and so on.
We've got some confidence with the technology now; we understand there's not one solution which fits all, we have to look around, take it from other industries and adapt it to our sector.
What are the key ingredients to sort of creating a ‘culture of safety’?
It's about taking the time to check in with people; talking and having conversations around safety, and also looking out for each other. Taking care of your own safety, but also the safety of the person beside you. And it’s not just about physical safety; we need to talk about mental health and remove the stigma around talking about it.
Mental health has touched my immediate family and I’m personally very familiar with it. I say to people in meetings that I'm not talking about mental health as an abstract concept; it's impacted my own family. I think people can then relate to that and think: “If it's happened to Larry, it could happen to me or my family.”
It’s ensuring the wider leadership team also speak about mental health and our people understand they care. Addressing mental health is core to a culture of safety. Unfortunately, people still feel they have to show up to work even though they're distracted or not in the right frame of mind because they still need a paycheque. I am sympathetic to that. But we need our frontline supervisors to understand what they should be looking out for when it comes to the welfare of their employees. Do they have the training to recognise when someone's in crisis? This is a big part of it. We’ve provided more training to our frontline supervisors so they’re equipped with the tools to recognise if there's an employee in crisis and get the professional help they need. Mining has long been a very macho industry and this behaviour impacts safety, so we’ve spent a lot of time encouraging our employees to stop and think about what they’re doing and speak up if something doesn’t feel right.
What’s your priority safety investment over the next 12 months?
We're embarking on more mental health training with our employees over the next year. From the standpoint of how we run our operations, we're investing more in technology by looking at how we can automate some of the manual processes at our operations.
Diversity is another area we’re invested. It’s well-established and researched that a diverse workforce is a safer workforce and a more effective workforce. Like I said, a lot of our processes are very manual. If we can eliminate the fact you don't have to be a 200-pound male to do a job by automating the process instead then it will go a long way to making our business more inclusive.
Related stories